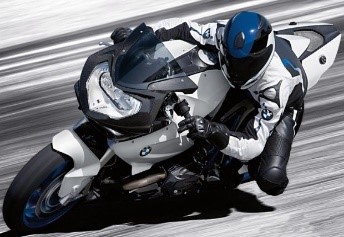
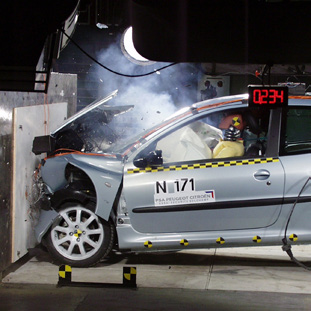
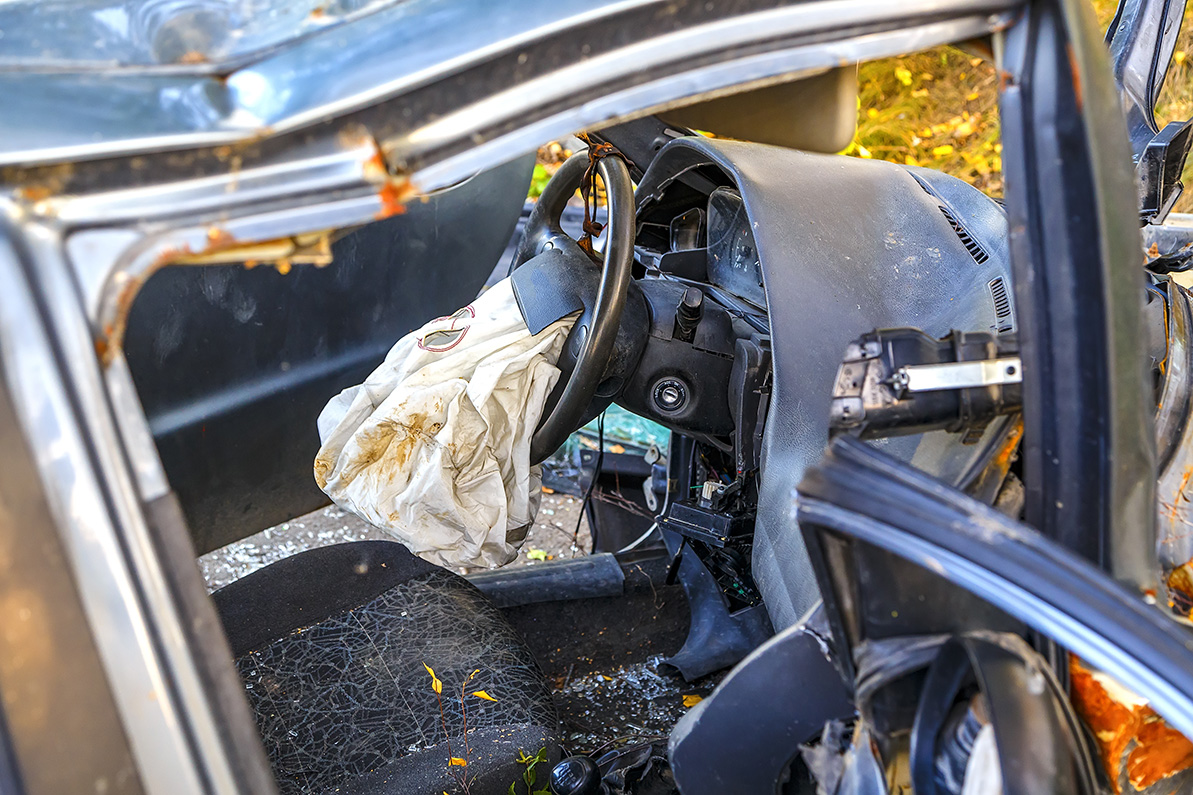
APPLICATIONS
- ESSAIS DE CRASH
- SÉCURITÉ DES PERSONNES VIA DES ESSAIS SUR TOUT OU PARTIE DU VÉHICULE ou MANNEQUIN
- PROTOCOLES D’IMPACT
- IMPACTS FRONTAUX ET CHEVAUCHEMENT
- ESSAIS DE PARE-CHOCS
- TEST AIRBAG – IMPACT LATERAL
- TESTS DE COLLISION AVEC UN USAGER FAIBLE (PIETON, CYCLISTE)
- HOMOLOGATION DES VEHICULES (TEST Euro NCAP)
Les essais de crash dans le secteur automobile consistent à tester le comportement des véhicules en cas de collision. On instrumente les véhicules, avec ou sans mannequin, en capteurs piézoresistifs qui permettent la mesure des chocs et des déformations en vue d’en étudier les conséquences sur le véhicule même et sur la sécurité des passagers.
Initialement focalisé sur la voiture, le terme « essai de crash » intègre désormais des essais piétons, cyclistes, et d’autres équipements non destructifs pour les systèmes de sécurité (e.g. ceintures et sièges pour enfants).
NOS SOLUTIONS POUR LE CRASH TEST
Depuis les débuts des tests de sécurité des véhicules, Endevco collabore avec les constructeurs automobiles, les manufacturiers (OEMs), les laboratoires d’essais et d’homologation, les concepteurs ainsi que les personnels de test des fabricants de mannequins anthropomorphiques (ATD) pour garantir des mesures précises des impacts avant, latéraux et arrière, des zones de déformation, de la sécurité des occupants à l’intérieur du véhicule et des piétons. Les accéléromètres piézo-résistifs à réponse en courant continu haute précision d’Endevco sont largement spécifiés dans ces applications en raison de leur conception à haute sortie, faible masse et taille compacte pour un montage dans des zones difficiles d’accès. Leur capacité de survie, leur petite taille et leurs capacités de mesure à réponse en courant continu offrent des solutions pour une gamme diversifiée de besoins en matière de tests automobiles.
- Conformité aux normes SAE J211, J2570 et ISO 6487
- Équipement standard sur tous les mannequins anthropomorphiques (ATDs)
- Sensibilité maximale
- Petit et léger
- Robuste jusqu’à 10 000 g
Notre technologie: le MEMS piézorésistif
MEMS signifie « système microélectromécanique » (de l’anglais MicroElectroMechanicalSystems). Les composants de ce système sont fabriqués en silicium pour les propriétés mécaniques de ce matériau (linéarité, hystérésis et endurance). Parmi les intérêts de cette technologie, les points forts sont sa dimension microscopique, son rendement et la possibilité d’automatisation des procédés de production.
La structure initiale est un disque de silicium, nommé « wafer » qui délivrera plusieurs composants.
Diverses opérations sont effectuées : dépose de couche, sérigraphie, soudure ; gravure, bains chimiques et cycles thermiques. En fin de production, aggloméré par étuvage, chaque composant prend un aspect « monobloc » dont l’épaisseur est proche d’un millimètre. Ils seront ensuite séparés par coupe.
Le MEMS dispose alors des propriétés d’un assemblage électromécanique mais dans une dimension microscopique qui n’a pas de jeu.
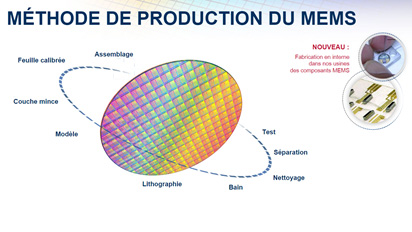
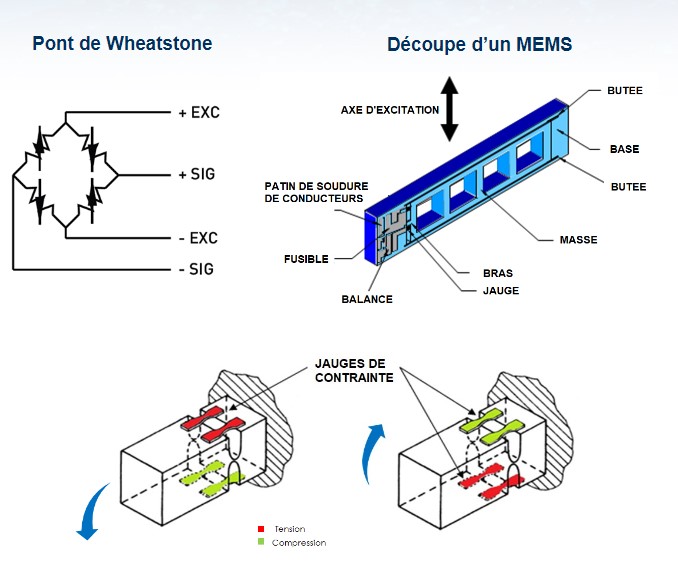
Les capteurs MEMS piézorésistifs sont assemblés en pont de Wheatstone. Inventé en 1833, Sir Charles Wheatstone rendit cette utilisation populaire en 1843. Il s’agit d’un circuit électrique passif, qui utilise des éléments résistifs variables (bras) dont le déséquilibre sera converti en signal. Le signal délivré (en milivolt (mV)) est proportionnel à la déformation mécanique des bras.
- Sous une contrainte constante (accélération ou pression), le pont envoie une information électrique stable et permet ainsi la mesure de sollicitations statiques et quasi-statiques.
- Comme le déséquilibre dépend de la déformation des bras, il n’y a pas de charge, la sortie analogique reflètera la contrainte sans délai ni décharge.
L’utilisation de la technologie piézoresistive est prédominante dans les applications de mesure du continu, de l’accélération statique, les mesure d’impacts et de très haut niveau de chocs.
Accéléromètres piézorésistifs pour mesures de chocs
CAPTEURS MONOAXIAUX – Amortis
CAPTEURS MONOAXIAUX – non amortis
CAPTEURS TRIAXIAUX
Documentation associée
Notes techniques
-
Mesures d’ondes de choc : technologies, Solutions
Téléchargez le guide en pdf Introduction Les mesures d’ondes de choc lors des essais d’explosion concernent aussi bien le secteur militaire que des industries mettant en oeuvre des conteneurs de produits inflammables ou explosifs. Trois grands types d’essai sont à distinguer: l’explosion à l’air libre, la déflagration canalisée et la déflagration en espace confiné :■… Découvrir
-
Essais d’impacts sur casques
Présentation ENDEVCO, en tant que spécialiste de la mesure de chocs et de vibrations, essaie toujours de présenter les technologies de capteurs, leurs fonctionnements, où sont leurs différences et aussi leurs avantages propres. Une de nos dernières démonstrations concerne les tests de choc sur les casques. Après un montage simple (instrumentation d’un casque de vélo… Découvrir
-
La technologie piézorésistive
introduction Le « Mems » est un microsystème électromécanique – en anglais « Micro Electro Mechanical Systems » qui est fabriqué à partir de matériaux semi-conducteurs. L’intérêt de cette technologie est sa dimension microscopique, de l’ordre d’une dizaine de nanomètres qui permet une intégration dans un composant miniature. L’assemblage de silicium et composants variés associés… Découvrir
-
Quelle technologie pour quel type de mesure ?
PCB Piezotronics propose trois grandes technologies pour couvrir vos essais vibratoires (du confort vibratoire au choc) & pression (de la mesure statique au blast). Chaque technologie a des atouts et des limitations spécifiques: il est ainsi important de se poser sur chaque essai pour définir quelle est la solution la plus adaptée – ou quelles… Découvrir
-
Mesures de choc: impacts de la technologie choisie et précautions à prendre
Mesure de chocs: quelle technologie de capteurs, quelles précautions dans la chaîne de mesure ? Découvrir
-
Technologie Piezoresistive et amortissement du capteur
Innovation: l’amortissement multimode damping pour les capteurs de choc piézorésistifs Découvrir
-
Les effets des câbles sur vos mesures
Les effets des câbles sur vos mesures Découvrir
-
Mesure de chocs mécaniques – Note technique d’Henri Grzeskowiak
Henri Grzeskowiak, propose une note technique résumant ses observations quant aux dérives provoquées par des chocs mécaniques. Ses analyses et conseils sont à lire ici. Découvrir
Livres blancs
-
Journee technique : Essais Ondes de Choc au laboratoire PRISME – INSA BOURGES
Journée Technique : essais ondes de choc au Laboratoire PRISME de INSA CVL – Bourges Découvrir
-
Essais biomécaniques en tennis : mesures d’impact et de vibrations avec des accéléromètres piézoélectriques et résistifs
Avantages et inconvénients des deux technologies dans le cadre de la mesure d’impacts sur une raquette de tennis. Découvrir
-
Homologuer les casques de moto ECE/ONU R22.06 grâce à des capteurs de choc et de vitesse angulaire – CRITT SL
Prise en compte de l’accélération rotationnelle et du critère de lésions cérébrales à l’occasion de chocs obliques lors de chutes de casque Découvrir
Brochures
-
Essais Automobiles
Découvrez nos solutions pour optimiser vos essais automobiles Télécharger la brochure
-
MesureS de choc
Découvrez nos solutions pour optimiser vos mesures de choc Télécharger la brochure
-
Essais Sécurité automobile – crash test
Découvrez nos solutions pour optimiser vos essais de crash Télécharger la brochure
-
Essais balistiques
Découvrez nos solutions pour oprimiser vos essais balistiques Télécharger la brochure